


The solution in this case was for the guy at Magma to just throw the punch itself onto the lathe and whack off the bottom most 4 threads. The solution would be either for the shorter die to be cut even shorter, or to bore out the bottom 1/8" or so of the inside of the die, or to get a longer punch. When I first got the new shorter die and the modified wider punch from Magma, it turns out that even extending the punch so far down that the threads on the punch were nearly in contact with the die, the bullets were still barely held in the die by less than 1/8", and I really needed them falling out in one stroke because of the fragile hollow point bullet tips. I wouldn't have minded if the recess were cut a little narrower, leaving a wider ring around the edge of the punch, but it's working fine and leaving no divot on the back of the bullets, so it's all good. 45 caliber sizing die, and also showing the face of this oversize punch having a recess cut into the face of it, so all the force is distributed into a ring around the outside of the punch, avoiding the casting nib often present in the center of a cast bullet. Here are a couple photos showing the wider than standard punch that's just a few thou under the inside diameter of the. It's working absolutely perfectly with my coated hollow point bullets. 45 bullets I've sized using this new, wider punch with the recessed center now have zero deformation or divot in the back of the bullet, and using the shorter die with no lube holes that they made for me to use with my coated bullets, the bullets I size go through an fall out the bottom of the press in a single stroke. All the pressure is now in a ring around the outside of the bullet. He threw the punch onto the lathe and drilled a little hollow recess in the center of the punch, so now it doesn't touch the center of the rear of the bullet (unless you get an "outie" casting nib that sticks out enough to contact the punch even in that recessed hollow). It will still be pushing against the casting nib in the center of the bullet unless you get them (or do it yourself) this next trick:
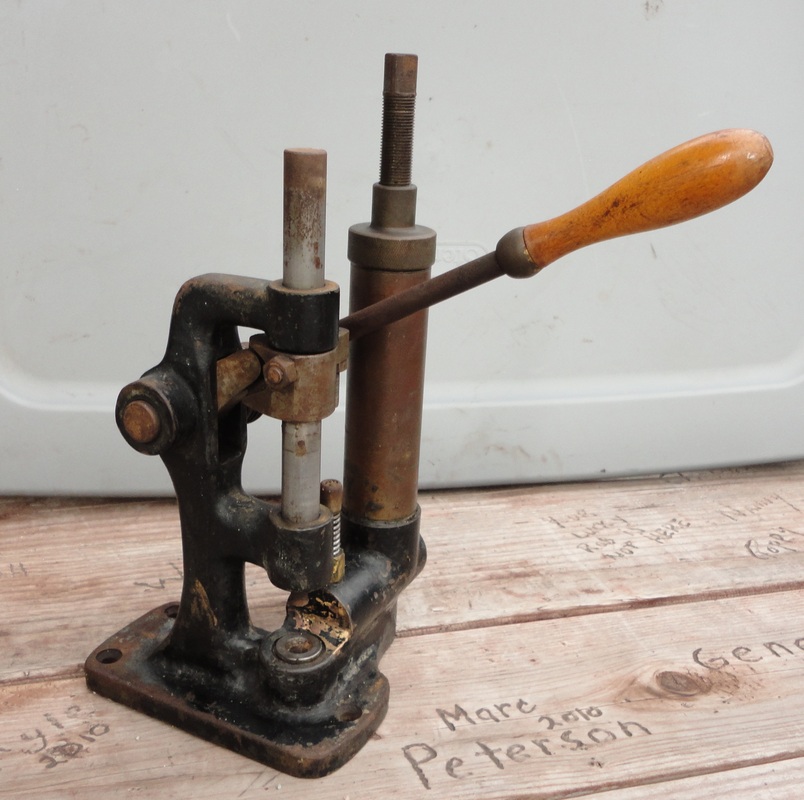
The pressure is now reduced so much over the bullet base that it avoids deforming it or leaving that divot. This spreads the force of the punch out over practically the whole base. Turns out Magma Engineering will sell you an oversized punch that is like 7 thou under the diameter of their. I also wasn't that pleased that all this pressure was being exerted on the casting nib on the back of the bullet, not necessarily on a flat bullet base. This was exacerbated by using the normal sizing die where each bullet had to push the previous bullet the rest of the way through the die, so the pressure of the standard punch on the rear of the bullet was leaving this divot. Not pure lead soft, more like wheel weight with a little pure lead mixed in sort of soft. 45 bullets enough pressure was being put onto the backs of the bullets that the punch was leaving a shallow divot on the backs of the bullets, particularly the softer ones I was using in my. 357 sized sizing die without contacting the die walls. That is, I'd only ever owned the standard punch for the Star sizer, and it's narrow enough that it can go into a 9mm or. This was necessary for me because I was now sizing these hollow point cast bullets, and the noses of these hollow points were too fragile to allow them to push the previous bullet the rest of the way out of the normal sizing die.Īnother problem I wanted to solve may or may not technically have been a real issue, but it was bugging me, and we solved it beautifully. This is so that you can push the bullets all the way through so they fall out the bottom in the same stroke, and don't require the next bullet to push them the rest of the way out. In talking with the lady at Magma I discovered that they'll sell you a version of their die that is much shorter than the conventional sizing die.
#Star luber sizer plus
I called up Magma Engineering (they sell the Star Sizer and all the dies and punches and whatnot, plus other mostly commercial casting type gear) to discuss some issues I was having sizing my coated bullets, in particular my hollow points that I cast using the mould I recently picked up from MP Moulds. This info wasn't really about coatings, so I thought it deserved its own thread. This is a break-away thread from another thread on powder coated bullets where a poster asked about sizing coated bullets through a Star sizer.
